CNC Turning Metal Part Factory: Revolutionizing Precision Manufacturing
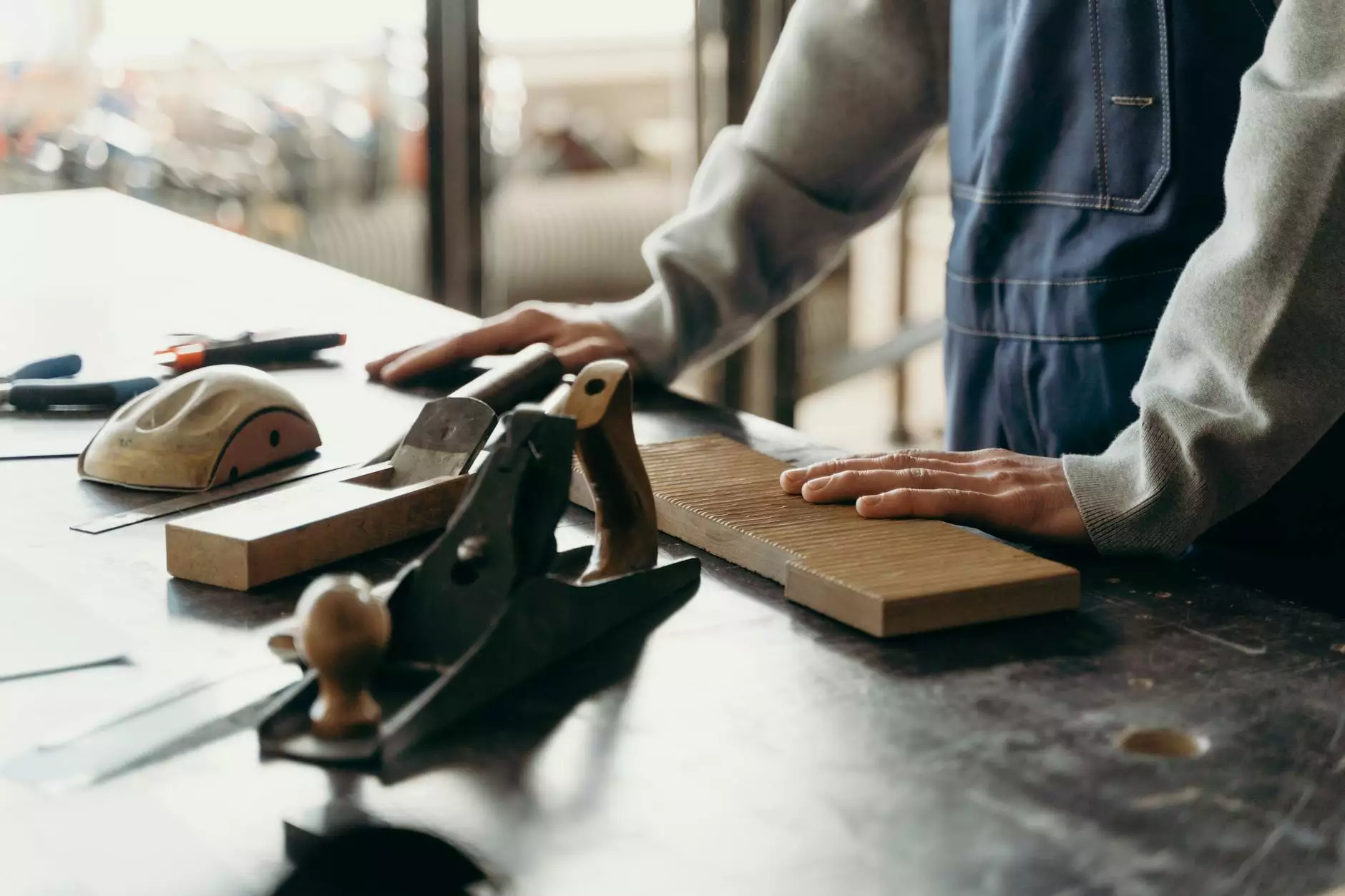
Understanding CNC Turning
CNC turning is a crucial process in the manufacturing industry that involves the precision machining of metal parts. Utilizing computer numerical control technology, these factories efficiently produce parts that meet stringent specifications.
The Significance of CNC Turning in Metal Fabrication
The role of CNC turning in the field of metal fabrication cannot be overstated. As industries demand higher precision and lower tolerances, CNC turning machines deliver consistency and repeatability. Here are some of the benefits of CNC turning:
- High Precision: CNC machines can achieve tolerances of +/- 0.001 inches.
- Increased Efficiency: Automated processes reduce cycle times and enhance production rates.
- Versatility: CNC turning allows for the fabrication of a wide variety of shapes and sizes.
- Reduced Waste: Advanced technology minimizes material waste, making the process more economical.
- Consistency: Each part produced is nearly identical, which is crucial for assembly processes in larger manufacturing operations.
How CNC Turning Works
The process of CNC turning begins with a designed computer model, typically created using CAD software. The following steps outline how a cnc turning metal part factory operates:
- Design Phase: Engineers create a precise 3D model using CAD software, detailing every aspect of the part specifications.
- Programming the CNC Machine: The CAD model is converted into a CNC program that will guide the machine during the turning process.
- Setup: Raw materials are secured in the machine, which is calibrated to the desired specifications.
- Turning Process: The CNC machine uses a rotating workpiece and stationary cutting tools to shape the metal part.
- Quality Control: Each finished part undergoes rigorous quality inspection to ensure it meets the required tolerances and specifications.
The Advantages of Partnering with a CNC Turning Metal Part Factory
Partnering with a specialized cnc turning metal part factory provides several strategic advantages for businesses in various industries, including automotive, aerospace, and electronics. Key benefits include:
- Cost-Effective Production: High volume machining can significantly reduce costs per unit.
- Expertise and Experience: Dedicated manufacturers possess specialized knowledge that leads to better quality output.
- Access to Advanced Technology: Factories often utilize the latest CNC technology, which improves production capabilities.
- Custom Solutions: Custom machining services allow businesses to receive tailor-made parts that fit precisely into their applications.
Maintaining Quality in CNC Turning Operations
Quality assurance in a cnc turning metal part factory is paramount. A rigorous quality control program ensures that each part meets the highest standards and specifications. Some essential practices include:
- In-Process Inspections: Continuous monitoring of the machining process for dimensional accuracy.
- Calibration: Regular calibration of machines to maintain precision and accuracy.
- Material Quality: Sourcing high-quality raw materials that adhere to industry standards.
- Final Inspection: Thorough inspections at the end of the production process to ensure all specifications are met.
CNC Turning Applications Across Industries
The versatility of CNC turning is reflected in its wide range of applications across various sectors. Here are some of the industries that benefit immensely from CNC turning processes:
- Aerospace: Manufacturing of critical components like turbine blades and structural parts.
- Automotive: Precision parts for engines, transmissions, and suspension systems.
- Medical Devices: Custom parts such as surgical instruments and implants.
- Electronics: Components for circuit boards and enclosures.
- Oil and Gas: High-strength components for drilling and extraction equipment.
Future Trends in CNC Turning Metal Part Factories
The future of CNC turning metal part factories appears promising as advancements in technology continue to reshape manufacturing. Key trends to watch for include:
- Increased Automation: Enhanced automation will lead to even faster production rates and reduced labor costs.
- Additive Manufacturing Integration: Combining CNC turning with 3D printing for hybrid manufacturing capabilities.
- Artificial Intelligence: AI will enhance predictive maintenance for CNC machines, minimizing downtime and optimizing operations.
- Sustainability: A push for eco-friendly practices will drive factories to reduce waste and use sustainable materials.
Choosing the Right CNC Turning Metal Part Factory
When it comes to selecting a cnc turning metal part factory, several factors should be considered:
- Experience: Look for a factory with a proven track record in machining parts for your specific industry.
- Technology: Ensure the factory uses the latest CNC technologies for optimal precision and efficiency.
- Quality Certifications: Verify that the factory holds necessary quality certifications such as ISO 9001.
- Customer Service: Strong communication and customer support are critical for addressing any potential issues.
Conclusion
A well-established cnc turning metal part factory can be a game-changer for businesses seeking to enhance their manufacturing capabilities. With its advanced technology, precision, and efficiency, CNC turning is at the forefront of modern metal fabrication techniques. To stay competitive, businesses must recognize the value that CNC turning can bring to their manufacturing processes and seriously consider partnerships with specialized factories. Embrace the future of manufacturing with CNC technology, and watch your production capabilities soar.