Understanding the Importance of Die Casting Mould Parts in Metal Fabrication
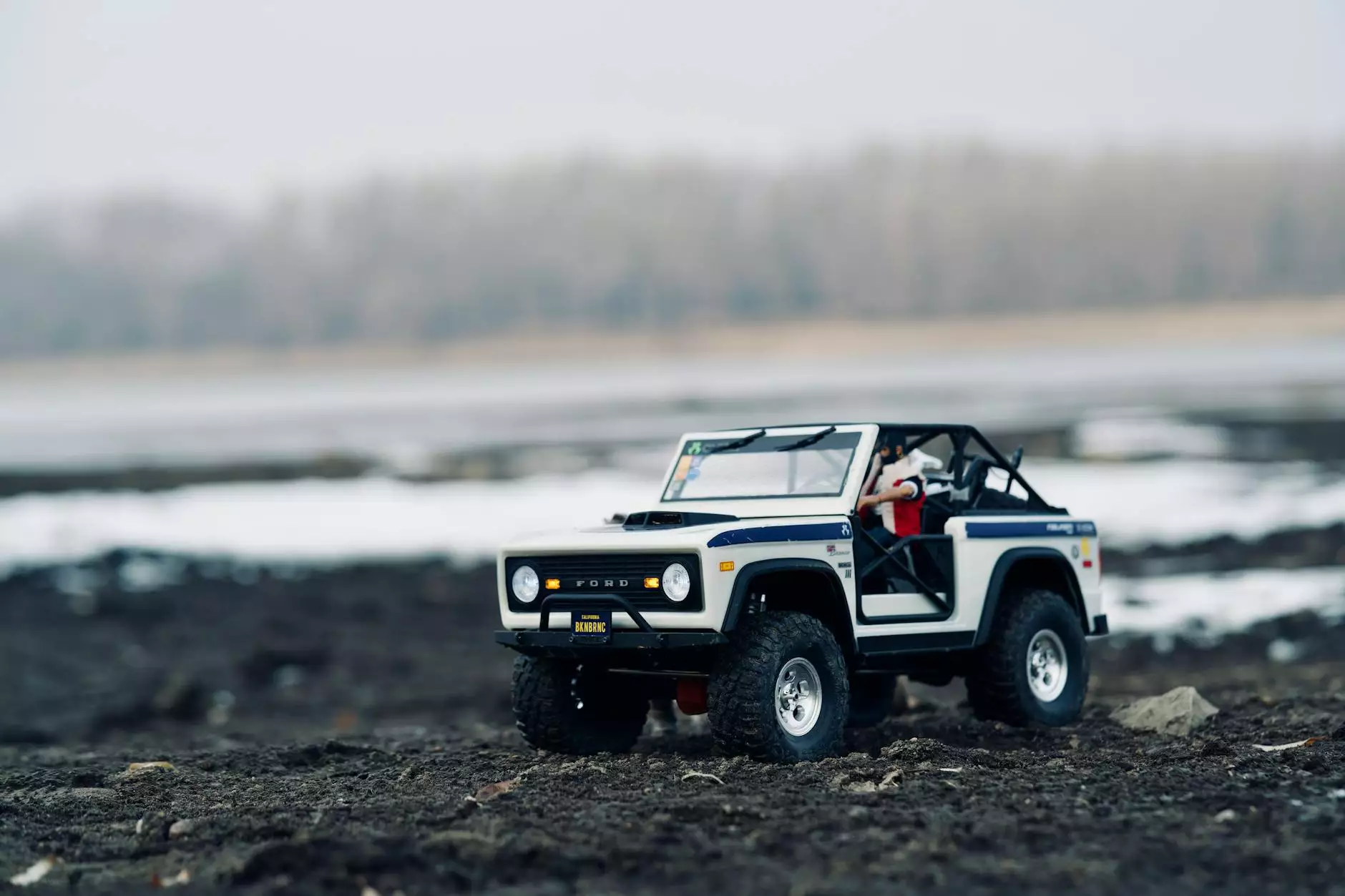
In today's competitive industrial landscape, the demand for precision and efficiency in manufacturing is at an all-time high. Among the various processes that facilitate precision manufacturing, die casting stands out as a leading method for producing high-quality metal parts. The core of the die casting process lies in its mould parts, which play a significant role in ensuring the reliability and quality of the finished product. This article delves deeply into the world of die casting mould parts, offering insights into their functionality, benefits, and the technology behind them.
What Are Die Casting Mould Parts?
Die casting mould parts are essential components used in the die casting manufacturing process. They are typically made from high-grade steel and are designed to create specific shapes and forms in the molten metal that is injected into the die. The precision of these mould parts directly affects the quality and accuracy of the finished products.
The Die Casting Process Explained
The die casting process involves several key steps:
- Preparation: The die, which consists of two halves, is prepared with the appropriate coatings to ensure easy release of the casted part.
- Melting: Metal is melted and prepared for injection into the die.
- Injection: The molten metal is injected into the die under high pressure to ensure it fills every cavity.
- Cooling: Once the metal has cooled and solidified, the die is opened to release the finished part.
- Trimming: Excess material is trimmed to give the part its final shape and finish.
Types of Die Casting Mould Parts
There are various types of die casting mould parts that serve different purposes throughout the die casting process. Key types include:
- Main Cavity: This is the primary section of the mould that shapes the final part.
- Core Inserts: Used to create internal features or hollows within the cast parts.
- Locators: These ensure proper alignment of the two halves of the die during closing.
- Cooling Channels: Designed to control the temperature of the die, enhancing production efficiency and part quality.
- Guide Pins and Bushings: These are critical for guiding the alignment of the die halves.
Applications of Die Casting Mould Parts
The versatility of die casting mould parts makes them suitable for a wide range of industries including:
- Automotive Industry: Producing complex components such as engine blocks, transmission cases, and wheels.
- Aerospace: Manufacturing lightweight, high-strength parts that meet stringent safety standards.
- Consumer Electronics: Crafting housings, frames, and fixtures that require precision and durability.
- Industrial Machinery: Creating components that contribute to the efficiency and longevity of machines.
Benefits of Using Die Casting Mould Parts
The use of die casting mould parts in manufacturing confers several advantages, making them a preferred choice for many applications:
- High Precision: Die casting allows for incredibly detailed parts with tight tolerances, reducing the need for secondary machining.
- Durability: Parts produced through die casting are strong and can withstand high levels of stress and strain.
- Efficient Production: The process is highly automated, allowing for rapid production cycles and reduced labor costs.
- Material Versatility: Die casting can be used with various metals such as aluminum, zinc, and magnesium, each chosen for specific properties.
How to Choose the Right Die Casting Mould Parts
Selecting the appropriate die casting mould parts is crucial for ensuring the success of the final product. Consider the following factors:
- Material Compatibility: Ensure that the mould material can withstand the metal being cast.
- Design Complexity: Choose moulds that can accurately produce the desired part shape and features.
- Production Volume: High-volume production may require more robust moulds capable of withstanding continuous use.
- Cost Considerations: Balance the upfront investment with the long-term benefits expected from the mould's performance.
Innovations in Die Casting Mould Technology
The field of die casting is constantly evolving, with new technologies emerging to enhance the production process. Some noteworthy innovations include:
- 3D Printing: Used for rapid prototyping of mould parts, allowing manufacturers to test designs before full production begins.
- Advanced Coatings: New coatings are being developed to improve the longevity of moulds and reduce maintenance needs.
- Smart Technology: IoT-enabled sensors can monitor die conditions in real-time, optimizing performance and minimizing downtime.
The Future of Die Casting Mould Parts in Metal Fabrication
As industries continue to demand higher efficiency and quality standards, the future of die casting mould parts looks promising. Advancements in materials science and manufacturing technologies will likely lead to even greater precision and performance in the casting process. With the integration of automation, AI, and machine learning, manufacturers can expect enhanced forecasting for production volumes, reducing waste, and optimizing overall operations.
Conclusion
The role of die casting mould parts cannot be understated in the realm of metal fabrication. As industries strive for innovation and improvement in manufacturing processes, understanding and utilizing high-quality mould parts becomes essential. By investing in advanced mould technology, businesses can enhance product quality, improve production efficiency, and reduce costs.
For companies looking to procure top-notch die casting mould parts, partnering with established metal fabricators like DeepMould can lead to superior outcomes. With a focus on quality and precision, DeepMould is poised to meet the evolving needs of the die casting industry.