The Importance of Injection Nozzles in Diesel Engines
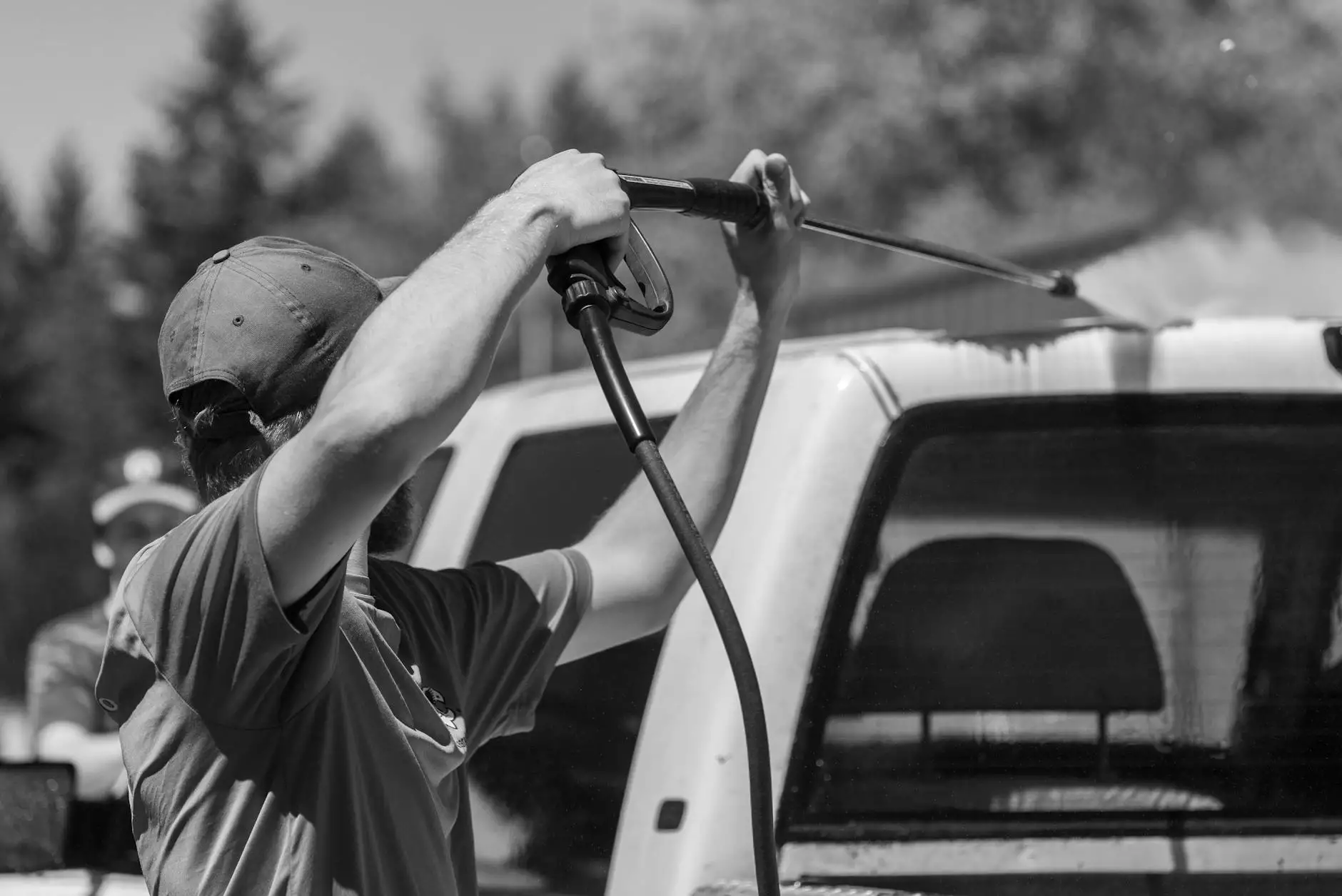
Understanding the Injection Nozzle in Diesel Engines
The injection nozzle in diesel engines serves as a key component that significantly impacts engine performance and efficiency. It is the part that delivers fuel into the combustion chamber at high pressure, atomizing it for effective burning. Understanding the function and importance of these nozzles is crucial for anyone involved in diesel engine maintenance, repair, or manufacturing.
How Injection Nozzles Work
Injection nozzles operate by utilizing high pressure to spray the diesel fuel in a fine mist. The process of fuel injection is highly synchronized with the engine’s timing, ensuring that fuel is injected at the optimal moment for combustion.
When the injector opens, a valve mechanism releases the pressurized fuel that atomizes as it exits through the nozzle’s tip. There are various types of injection nozzles, including:
- Single-hole nozzles
- Multi-hole nozzles
- Centrifugal nozzles
The Types of Injection Nozzles
Choosing the right injection nozzle in diesel engines is essential for optimal engine performance. Here are the main types:
1. Single-Hole Nozzles
These nozzles focus on a single spray pattern, providing a precise injection of fuel. They are generally used in older engine models and in applications where fuel efficiency is not as critical.
2. Multi-Hole Nozzles
More modern engines often use multi-hole nozzles. These injectors spray fuel in multiple directions, which improves atomization and enhances combustion efficiency. This design significantly reduces emissions and enhances power output.
3. Centrifugal Nozzles
Utilized primarily in high-performance applications, centrifugal nozzles can handle greater flow rates. They are tailored for applications where high power and torque are necessary, such as in commercial or heavy-duty diesel engines.
Key Functions of Injection Nozzles
Understanding the functional role of the injection nozzle in diesel engines can greatly impact maintenance and performance optimization. Key functions include:
- Fuel Atomization: Proper atomization allows for better mixing with air, leading to more effective combustion.
- Fuel Delivery: The nozzle must deliver the right amount of fuel at the right time, crucial for engine efficiency.
- Cooling: In high-performance settings, injection nozzles can provide a cooling effect during combustion.
Impact of Injection Nozzles on Engine Performance
The choice and condition of the injection nozzle in diesel engines affect various aspects of engine performance:
1. Fuel Efficiency
Efficient fuel atomization leads to more effective combustion, contributing to lower fuel consumption. Well-maintained nozzles optimize this process, ensuring that engines run at peak efficiency.
2. Power Output
As fuel quantity and spray pattern play a critical role in power generation, the correct nozzle type can significantly enhance the power output of a diesel engine.
3. Emission Control
Modern diesel engines with efficient injection systems lead to lower emissions of pollutants. Multi-hole nozzles, in particular, help meet stringent emission standards set by regulatory bodies.
Maintenance of Diesel Injection Nozzles
Regular maintenance of the injection nozzle in diesel engines is vital for sustaining its performance and extending the life of the engine. Key maintenance practices include:
- Regular Inspections: Check for wear and tear, and ensure that the nozzles are clean and functioning properly.
- Cleaning: Use precision cleaning methods to remove carbon deposits that can hinder performance.
- Testing: Conduct testing for nozzle pattern and spray characteristics regularly to ensure optimal injection.
Common Issues Faced with Injection Nozzles
Despite careful maintenance, diesel injection nozzles can encounter several common problems:
1. Clogging
Dirt, carbon, and fuel deposits can clog the injector, leading to poor engine performance and increased emissions.
2. Poor Fuel Spray Pattern
If the nozzle does not spray fuel correctly, it can affect the combustion process, resulting in reduced power and increased fuel consumption.
3. Leaking Injectors
Leaking injectors can lead to fuel wastage, loss of power, and decreased fuel efficiency.
Advanced Technologies in Fuel Injection Systems
With the advent of technology, injection nozzles in diesel engines have seen significant advancements. Innovations in fuel injection systems include:
- Common Rail Systems: These allow multiple injections per cycle for improved performance.
- Electronic Control: Modern engines utilize electronic fuel injection to optimize the timing and amount of fuel delivered.
- Variable Geometry Nozzles: These can adjust their spray pattern based on engine load and speed, ensuring optimal performance.
Conclusion
In summary, the injection nozzle in diesel engines is an indispensable component that directly influences performance, efficiency, and emissions. By understanding its functions, types, and the importance of proper maintenance, diesel engine operators can ensure their engines run smoothly and efficiently. Investing in quality injector components and adhering to maintenance schedules will significantly prolong the life of a diesel engine and ensure optimal performance.
For high-quality diesel engine parts and expert advice, visit client-diesel.com. Your trusted source for diesel engine performance solutions!