Understanding Dip Molding Materials
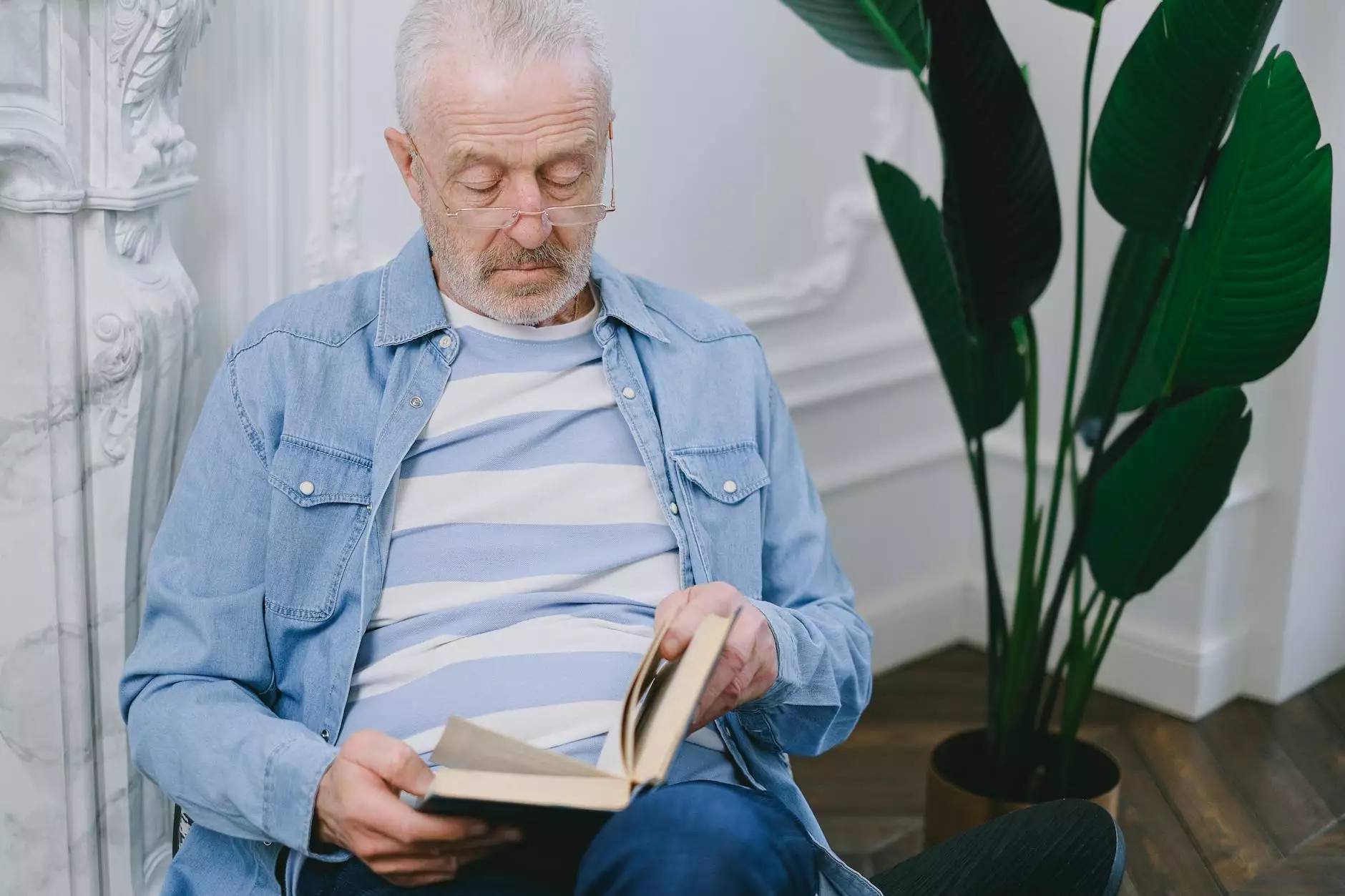
Dip molding materials have emerged as a crucial component in various sectors, particularly in the fields of electronics and medical supplies. This innovative manufacturing process allows for the creation of custom parts and components that meet specific industry standards and demands. In this article, we will explore the intricacies of dip molding materials, their applications, benefits, and much more.
What is Dip Molding?
Dip molding is a specialized manufacturing process where a part is dipped into a liquid material, usually polymer, creating a coating or forming a shape that hardens upon cooling. This technique is widely used to produce protective coatings and functional components for a variety of applications. The versatility of this process makes dip molding materials essential in industrial production.
Types of Dip Molding Materials
There are several types of dip molding materials used in the process, each with unique properties that make them suitable for specific applications:
- Polyvinyl Chloride (PVC): Widely used for its durability and flexibility, PVC is ideal for producing grips and protective layers.
- Polyurethane (PU): Known for its excellent abrasion resistance, PU is frequently utilized in high-wear applications.
- Silicone: This material is perfect for medical applications due to its biocompatibility and resistance to extreme temperatures.
- Rubber: Often used for gaskets and seals, rubber materials provide excellent sealing properties and flexibility.
The Process of Dip Molding
The dip molding process can be broken down into several key steps:
- Preparation: The object to be molded is cleaned, coated with a release agent, and prepared for dipping.
- Dipping: The prepared object is submerged into a tank containing the liquid dip molding material.
- Draining: After a predetermined time, the object is removed, and excess material is drained back into the tank.
- Curing: The dipped component is then allowed to cure or harden, either at room temperature or in an oven, depending on the material used.
- Finishing: Finally, any additional finishing processes, such as trimming or surface treatment, may be applied to achieve the desired specifications.
Applications of Dip Molding Materials
Dip molding materials find their application in several domains, including:
1. Electronics Industry
In the electronics sector, dip molding materials are essential for creating protective coatings for electrical components. This process is vital for:
- Insulation of wires and connectors, preventing short circuits.
- Providing grips and non-slip surfaces on tools and devices.
- Creating durable housings for electronic devices to withstand environmental factors.
2. Medical Supplies
Dip molding plays a critical role in the medical supplies industry, as the materials used must meet stringent safety standards. Applications include:
- Manufacturing ergonomic handles for surgical tools.
- Creating protective coatings for medical devices.
- Producing patient-friendly grips and handles that enhance usability.
Benefits of Using Dip Molding Materials
Utilizing dip molding materials offers numerous advantages that contribute to their popularity across industries:
Cost-Effective Production
Dip molding allows for bulk production, which can significantly reduce manufacturing costs. The process is efficient, requiring less material waste and minimal labor, resulting in lower overall expenses.
Customization and Versatility
One of the significant benefits of dip molding is the ability to customize components to meet specific needs. Various sizes, shapes, and colors can be achieved, making dip molding materials suitable for a wide range of applications.
Durability and Protection
Products made with dip molding materials tend to be more durable and protected against environmental factors, such as moisture, chemicals, and abrasion, ensuring longer life spans for manufactured goods.
Improved Ergonomics
In industries like medical supplies and electronics, the ergonomic design made possible by dip molding improves usability and functionality, resulting in a better experience for end users.
Choosing the Right Dip Molding Materials
Selecting the appropriate dip molding material is vital for achieving desired results. Here are some considerations:
1. Application Requirements
Understand the specific demands of your application. For example, a medical device requiring biocompatibility will necessitate silicone, while a tool grip may be best served by polyurethane.
2. Environmental Factors
Consider the environment in which the final product will be used. Heat, moisture, and exposure to chemicals can all influence material choice.
3. Cost vs. Performance
Evaluate the balance between cost and performance. While some high-performance materials may be more expensive, they can save costs in the long run by enhancing product durability and effectiveness.
Future Trends in Dip Molding Materials
The landscape of dip molding is constantly evolving, driven by technological advancements and market demands. Here are some trends to watch:
1. Sustainable Materials
With growing environmental concerns, there’s a push towards sustainable and recyclable dip molding materials. Manufacturers are exploring bio-based polymers and eco-friendly options.
2. Advanced Customization
Increasing demand for personalized products is encouraging innovations in dip molding technology, allowing for even greater customization possibilities.
3. Integration of Smart Technologies
The electronics industry is witnessing a rise in smart connected devices. Dip molding materials that integrate sensor technology will become more prevalent, enabling new functionalities.
Conclusion
Dip molding materials represent a dynamic and versatile facet of modern manufacturing, significantly impacting industries such as electronics and medical supplies. Their benefits include cost-effectiveness, customization, durability, and improved ergonomics, providing a strategic advantage to companies utilizing these materials. As trends shift towards sustainability and advanced customization, the future of dip molding looks promising, ensuring that it remains a vital component in the manufacturing landscape.
For more insights into how dip molding materials can enhance your business, consider exploring the offerings from trusted suppliers like nolato.com, where innovation meets reliability in manufacturing solutions.